The advantages of prototyping with CNC machining
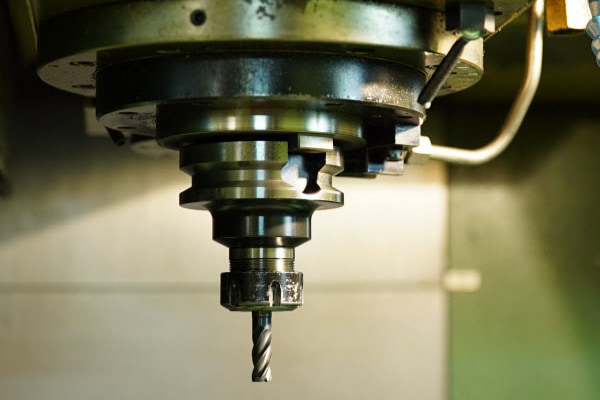
While many customers now consider 3D printing as the preferred method of rapid prototyping, CNC machining is still an important process for creating prototype parts.
As customers require various specifications and designs, it’s beneficial to consider the different forms a prototype can take and assess if prototyping is the best choice for your next project.
We take a look at the advantages of prototyping with CNC machining and what these benefits can mean for customers and businesses.
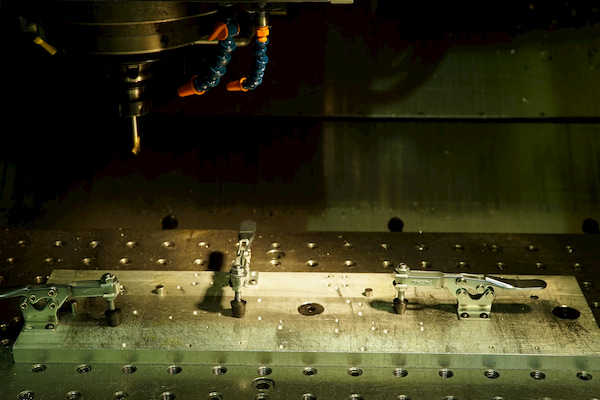
THE APPLICATIONS OF PROTOTYPING
Prototypes have many unique functions. At their most basic, prototypes act as placeholders — loose representations used to convey visual information about how the final part will look or behave.
These placeholder prototypes can be used to guide the research and development process or provide proof of concept.
And at their most ambitious, a prototype can also be used to pitch a new product to potential investors.
Some prototypes can also be used beyond visual representations. Customers may need to create engineering prototypes or production prototypes. These prototypes not only possess the visual proof but can function and act as a substitute for the real product.
So while 3D printing is a great option for visual prototyping, CNC machining is often preferable for functional prototypes that require strength, mechanical stability or other characteristics.
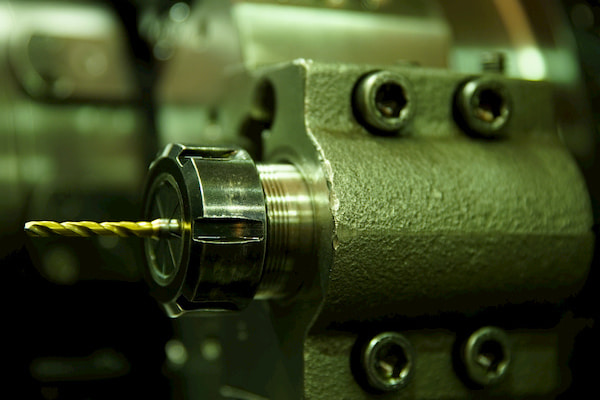
THE REASONS WHY YOU SHOULD CHOOSE CNC MACHINING
There are numerous reasons why customers may choose CNC machining to produce a prototype.
We break down the key advantages of prototyping with CNC machining, including speed of production, part quality, material options and similarity to the final part.
1. From file to prototype
Since CNC machining is a digital process that creates a part from a computer file, engineers know that a machined prototype will closely match the digital 3D design, and that the same digital design can later be used to create a final part with identical dimensions. This means the degree of repeatability is particularly high.
Using digital 3D designs also allows for quick and precise alterations. If a machined prototype exhibits a physical flaw resulting from bad design, the engineer can return to the CAD software to make suitable changes for the next prototype.
Different versions can be compared side by side, and simulation software can even be used to pre-emptively test how a part will perform in the real world.

2. Quality and consistency
Computer-controlled machinery tends to function exactly as it’s supposed to — until it breaks down. While many prototyping processes rely on human skill (and are therefore susceptible to human error), CNC machines follow their instructions to within a fraction of a millimetre.
They can also process over and over again. While a company might only make a single prototype, a CNC machine can run the same job a second time with minimal deviation from the first.
This is incredibly useful for developing new iterations of a prototype and for moving to production with the same machinery.
3. Range of strong materials
CNC machining not only offers a wide range of compatible materials, it also offers some extremely strong and durable materials.
Common CNC machining materials include:
- Aluminium
- Steel
- Stainless steel
- Magnesium
- Titanium
- Zinc
- Brass
- Bronze
- Copper
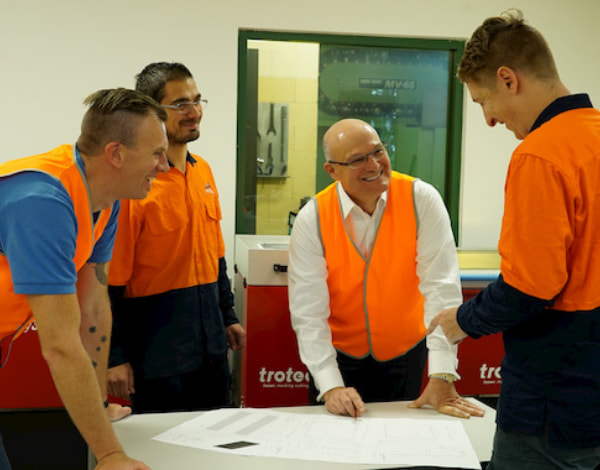
THE METAL SOLUTIONS EXPERTS
CNC machining can be an excellent choice for prototyping, but its suitability depends on the nature of the prototype.
It’s important to consider the purpose of the prototype and the materials that will be used in the process.
At Sevaan Group, we’re experts at metal solutions and we have the knowledge and experience to guide our customers on the best prototyping process for any project. We apply precision accuracy to ensure your product meets specifications.
We can also analyse and optimise the production process and fully test your product so you can move into production with confidence and certainty. Our process is tightly controlled and documented by our Quality Management and ERP systems.
Our CNC machining department also provides both horizontal and vertical milling, as well as five-axis turning. We use the latest automatic bar feeding technology to ensure we achieve the highest productivity for every product.
So, if you’re looking for precise, accurate, consistent and reliable quality, contact our highly skilled team of engineers today.