How has laser cutting evolved and where is it going next?
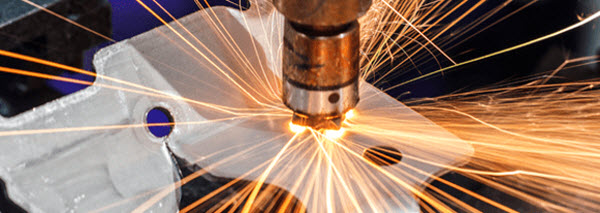
There’s no doubt that laser cutting has revolutionised industrial manufacturing.
It has made the process of cutting materials, especially sheet metal, far more efficient and accurate.
There are two main types of laser cutting:
- Fusion Cutting – This process involves fusing the material with a laser beam and applying a jet of high-pressure nitrogen to remove the excess molten material.
- Oxidation Cutting – The material is heated to the temperature of combustion. The material is then oxidised, removing the excess molten material.
These processes have been refined and tweaked over the years, and technological progress has made the process speedier, more energy efficient, and more accurate than ever before. In this article, we’ll take a look at how we got to this stage and what the future is likely to hold for laser cutting.
A Brief History of Laser Cutting
Laser cutting has come a long way since the earliest attempts at using hot laser beams to cut sheet metal in the 1960s, which saw engineers and physicists working together to create new industrial processes. In 1964, physicist and electrical engineer C. K. N. Patel invented the carbon dioxide laser, opening the door to using lasers for industrial cutting and manufacturing.
By the 1970s, carbon dioxide lasers were being used for intricate manufacturing work such as welding clock springs and welding the cathode components for early colour televisions. The increased precision and hands-free operation of lasers made them very attractive for delicate manufacturing work and allowed mass-production of these parts.
By 1979, a hybrid punch and laser machine had been developed, using CO2 to produce 500 Watts of power. This machine was used to cut sheet metal and could be programmed by the operator to cut precise curves. This was a breakthrough in the progress of laser cutting. Manufacturers were excited by the technology, and it didn’t take long for automobile and aerospace manufacturers to get involved and commission research and development. By the mid-’80s some early adopters began to introduce lasers on factory floors, but the limited power meant they were only good for small-scale production.
The 1990s was probably the golden age of development in laser cutting. In 1991, Haas Laser released details of a 2KW solid-state laser. This massively increased power meant more productivity. Now it was possible to use lasers to create large volumes. The age of laser-cutting in mass production had arrived.
By 2002, the automotive and aerospace industries were fully on-board with laser cutting technology, and 4KW solid-state lasers were becoming a common sight on factory floors. 2005 saw the development of a functioning short-pulse laser, making micromachining possible and leading to the highly efficient and fast machines that we see today.
The Future of Laser Cutting
The global laser cutting market is expected to grow to an incredible $6.72 billion by 2024 according to Grand View Research. This huge growth in demand has led to rapid innovation and investment in software and technology.
The biggest change in recent years has been the increased automisation of laser cutting machinery. Integrated software systems are now available that can take a 3D design, automatically produce a program and feed it to robotically controlled lasers. Intricate products and parts can now be manufactured more quickly and precisely than ever before.
The trend for increasing automation is likely to continue apace with the advent of the 4th Industrial Revolution, Industrial Internet of Things (IIoT) and smart technology. IIoT sensors are likely to make industrial laser cutting even more accurate, working to near-zero tolerances.
The applications of laser cutting are also expanding as the technology progresses. Now that more accuracy is possible, architects and designers are using lasers to produce intricate, even beautiful constructions such as decorative cladding, balconies, and balustrades.
The innovative use of a direct beam powered by high-performance diodes has increased the power of laser cutting, and it’s likely that Direct Diode Laser (DDL) technology is going to overtake solid-state and pulse lasers. Research has shown that DDL cuts 15% faster than other methods for most materials, and a massive 30% increase in speed when cutting aluminium sheet metal.
For enquiries or to speak to one of our experts, please click here