From Anvil to AI: a Sevaan Group History - and future - of smart metal manufacturing
People have been working with metal for millennia. It’s a skill that humans developed – some historians estimate – as far back as 8000 BC. There have been several major developments in metal manufacturing over the years… and one of the most intriguing is happening right now.

Jim Tzakos, Sevaan Group Co-Founder and Chief Executive Officer, has seen manufacturing boom in the last 20 years, but believes the most recent decade has been one of the most significant.
“With Industry 4.0 we have seen a surge in software integration into traditional machines.
People were creating software for the industry 20 or 30 years ago, but it’s only been in the last 10 years that we’ve had the technology for it to work directly with machinery – and that has seen incredible outcomes.”
As an early adoptee of Industry 4.0 technology, including system integration and robotics, Sevaan Group is already seeing more streamlined, more efficient and much more cost-effective metal fabrication and machining. With this in mind we thought we’d also take a look back at the history of metal manufacture, to see how recent developments fit into a very long – and fascinating – history.

Ancient metal origins
Metalwork has been a mainstay of nearly every civilisation on earth since humans first discovered how to extract it from the ground.
The earliest metalworkers in the Middle East and Asia worked with naturally occurring metals like gold, silver and copper. And to do that they developed a range of techniques – such as smelting (removing the metal from its ore), cutting, hammering, embossing and inlaying – that are the foundations of processes still in use today.
Throughout ancient history – and across the globe – artisans shaped gold into jewellery, decorative items and utilitarian pots; copper was used for tool and implements; and the first coins in the Western World were made of electrum, a naturally occurring alloy containing gold and silver.
Gold, silver and copper are soft metals so were easy to cut and shape – but their practical use was limited. The evolution of metalwork took a huge leap once humans learned how to mix metals. One of the first – and most significant – was bronze, which is a mixture of copper with tin or another secondary metal.

The major metal ages
One way of classifying early history is via the three-age system – the Stone Age (dating from around 2.5 million years ago), the Bronze Age and the Iron Age.
The Bronze Age began around 3000 BC when people discovered that mixing other materials with copper made it much stronger, harder and more durable. This led to more sophisticated tools and the first swords. The Iron Age commenced around 1000 BC with the earliest production of iron-based objects in Asia and Europe – and this was a game changer.
The earliest metallurgists discovered that a small amount of carbon added to iron could increase its strength enormously, and it became the metal of choice for weaponry, including swords, shields and armour. The first cast iron also appeared.
Other interesting metal ‘moments’ in pre-history include the discovery of mercury in China and India in approximately 2000 BC and the development of lead, which some estimate as early as 9000 BC. The Romans were particularly fond of lead and used it in everything from roofing to building ornaments and even – although less frequently – for coffins.

The not so humble blacksmith
Think metal manipulation throughout history and many people picture the blacksmith.
While they are most associated with the middle ages, blacksmiths have spanned thousands of years – and hobby blacksmithing has had a resurgence.
It’s believed blacksmiths stemmed from the Hittite civilisation around 1500 BC.
Ancient blacksmithing had somewhat erratic results, given the lack of comprehensive understanding around metal properties, but it took a leap during the Medieval period.
During the Medieval years, blacksmithing was a primary mechanical art. Now, with advanced skills in heating techniques and a better understanding of metal properties, the village blacksmith could readily produce tools, pots and pans, armour and weapons. Blacksmiths were highly regarded and, with their anvils and hammers, were a mainstay of every community.
Blacksmithing continued for hundreds of years, but as societies moved into the industrial era, demand for one-off workmanship declined. Machinery and mass production heralded a new age in metal manufacturing.
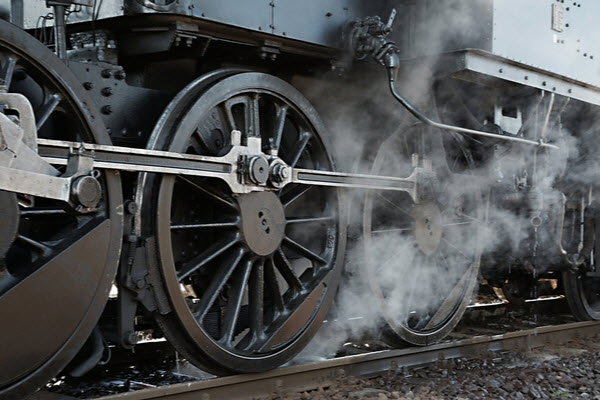
Moving into manufacture
Great Britain in the 1700s was on a roll. Thomas Newcomen invented the first steam engine in 1712, a weaving machine known as the Flying Shuttle mixed things up in 1733, and assorted developments over the remainder of the decade included the Spinning Jenny and Spinning Mule machines for cloth production, the first steam-powered locomotive in 1801 and even a new unit of measurement: the horsepower.
It was the first industrial revolution, with the development of the coal, iron, railroads, steam and textiles industries and huge growth in mechanical machinery. Starting in the UK in the mid-18th century, the industrial revolution would sweep the globe… and need lots of metal. Metal manufacture and sheet metal fabrication took a leap with the development of machines to cut, form and join metals – and the emergence of steel production.
Prior to 1860, steel was expensive so used infrequently. Things changed with the development of the crucible steel technique by Benjamin Huntsman in the 1740s, the Bessemer process in the 1850s and the Siemens-Martin process in the 1850s and 1860s – all methods for mass steel fabrication.
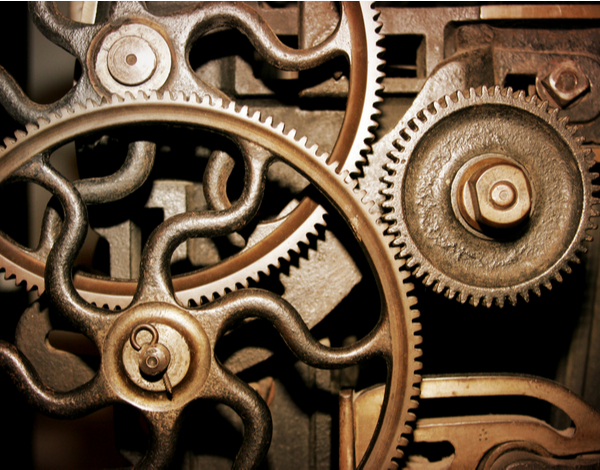
The Second Industrial Revolution
Increased opportunity for steel manufacture preceded the second industrial revolution.
It was a rapid industrialisation phase that started towards the end of the 19th century and continued through the beginning of the 20th century.
Also called the technological revolution or the age of science, it featured major breakthroughs in communication technologies – and significantly, electricity.
The first power station appeared in Britain in 1881. It had an incredible impact on the way people lived – and on how they worked.
Steel production flourished during the second industrial revolution. Stainless steel was developed in the 1910s which led to mass stainless steel production, and new techniques meant you could now manufacture interchangeable parts. Steel production directly impacted transportation in particular, with widespread metal manufacture of cars, planes, railroads, ships, construction projects and industrial machines.
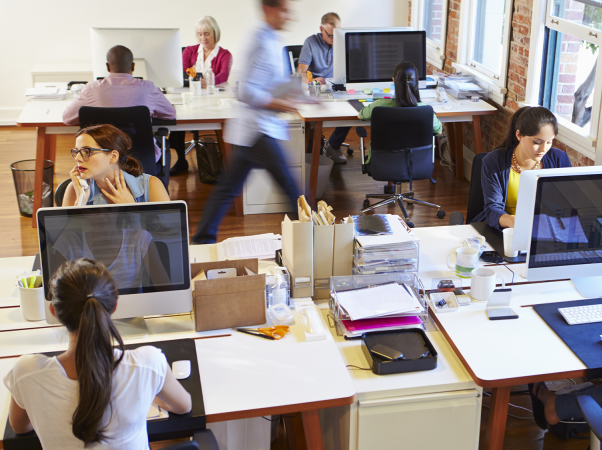
The Third Industrial Revolution
Over the last century, metal manufacturing techniques have developed dramatically, namely with the third and fourth industrial revolutions. The third industrial revolution began in the 1950s with the emergence of new forms of communication and rapid changes in information sharing. It saw the development of semiconductors, mainframe computing, personal computing and then the Internet – and from there, the emergence of analogue into digital technologies.
The move from analogue electronic and mechanical machines to digital technology during the 80s, 90s and 2000s was enormous. It changed the way people lived, worked, communicated and travelled. Digital technologies, including information technology (IT) and automation, transformed global communications… and metal manufacturing.
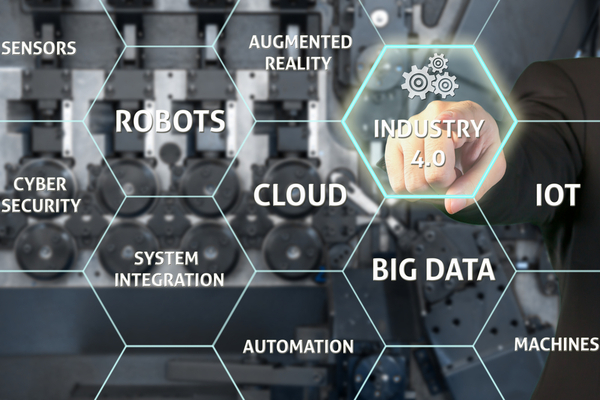
Industry 4.0 and the Internet of Things
Hot on the heels of the third industrial revolution is the fourth, more commonly called Industry 4.0. And at the centre of 4.0 is the Internet of Things (IoT), which is the addition of digitised and networking technologies to existing machinery and infrastructure.
And while Industry 4.0 is about digitalisation and automation, it’s also about connection.
It connects the physical and digital worlds, brings company and client closer, and encourages collaborations that will reap major benefits in advanced manufacturing – and superior steel fabrication solutions.
Industry 4.0 is new-generation technology capable of transforming operations and outcomes. And it can take various forms. It might include advanced automation, robotics, machine-to-machine and human-to-machine communication… or artificial intelligence.
Practical applications include tools like 3D printers, robotic arms for manufacturing processes or, simply, advanced touch interfaces on traditional metal machines. It’s changing the face of many industries, bringing company and clients closer and leading to improved economic competitiveness in a global market.

21st Century developments
And while 3D printers and artificial intelligence offer incredible potential for the future of advanced manufacturing, there have been certain developments over the years that still contribute to exceptional design for manufacturing and precision metal machining today – including laser cutting and CNC machining that both date from the 1960s. While the basic premise has stayed the same, the machines have changed significantly.
“The metal laser cutter, CNC plasma cutter, CNC lathe and other CNC machines have been around for quite a while, but they have become a lot more sophisticated in recent years,” says Jim, “and that has led to better metal manufacturing and a lot more efficiency for manufacturing companies and clients.”
Welding is a prime example of innovation that has stood the test of time. While a rudimentary style of welding was around in the Bronze Age, modern welding appeared in the 1800s. And now we use robotic welding at Sevaan Group, which eliminates human error and provides a safer, faster and more precise method of welding and metal fabrication.
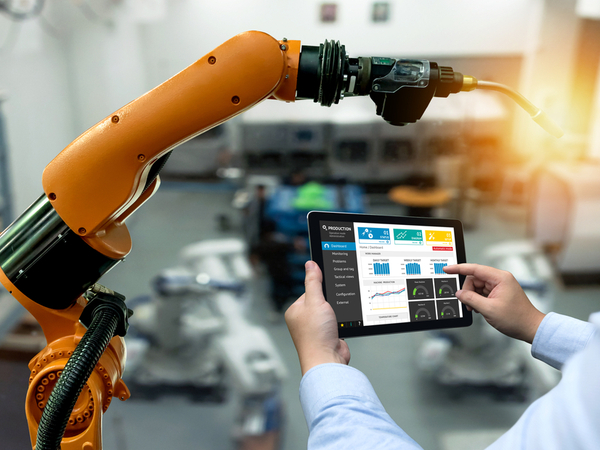
When traditional meets technology
For Jim Tzakos, the most significant changes have been with software development and digitisation. “Software for manufacturing and business processes was developed in the 1970s. It got more sophisticated and more flexible through to the 90s, and we saw the introduction of useful tools like material resources planning software. The problem with much of this software however was that it still relied on manual input.”
That’s changed. “With the introduction of the Internet of Things, the manual aspect has gone,” continues Jim. “So instead of seeing masses of spreadsheets which might be useless if there was a single error, we now have software that speaks directly to machines to calculate costings, timeframes and machine efficiency with 100% precision.”
Another benefit Jim sees is the ability for faster and more flexible manufacturing. “Look at set up times,” suggests Jim. “In the automotive industry for instance, it now takes 12 minutes to make a change to a huge machine, where it used to take hours in the 1980s. What really assisted this was getting to the stage where software links directly to machinery, including sheet metal machining.”

System Integration for Sevaan Group
The process Jim is referring to is system integration. And it’s a perfect example of the way machines meet – or talk to each other. Very simply, system integration might be the addition of a new technology – such as software – into current workplace machinery or systems.
Digitalisation technologies such as these are impacting metal fabrication and other industries globally. The result is smarter, faster and even more precise metal manufacturing processes.
Jim has been watching Industry 4.0 develop over many years – and he believes software is making the biggest impact. Here at Sevaan, we’re integrating new software into our ERP (Enterprise Resource Planning) system, which tracks all business functions.
“We installed our ERP system four years ago,” says Jim. “We’ve spent tremendous amounts of time and money implementing it and now it’s delivering excellent results, so we don’t want to start from scratch.” What we do want is seamless integration – to install complementary software that ideally also provides multiple benefits.
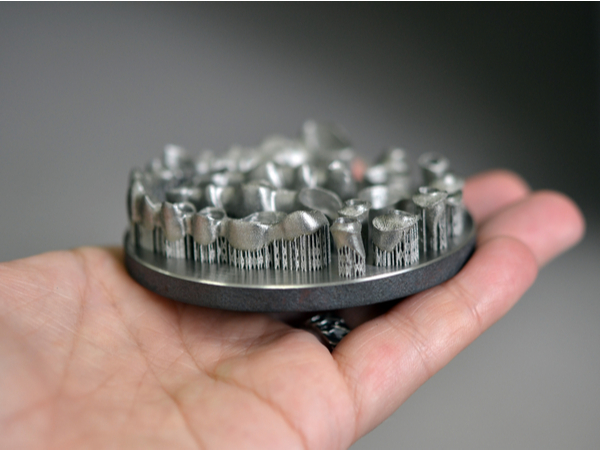
So, where to next?
The history of metal fabrication and machining has been one of growth and evolution. Industrial revolutions have been termed disruptors, because they turn the status quo on its head – and lead to something newer and significantly better.
So, where to next?
Jim suggests looking to Europe for the answer. “Europe is so far ahead in steel fabrication and metal machining. Companies like Bosch and Siemens have been key drivers of Industry 4.0.
We don’t know yet what will happen yet, but there may be evidence in the next five to ten years. Personally, I think the future of metal machining may lie with 3D printing… but mass production of 3D produced parts is still a fair way off. It’s exciting to think where we will go. And it’s exciting for our team, too, with the prospect of upskilling to operate these new technologies.”
From the anvil to AI, one thing is certain. Change has brought incredible opportunity for companies and for clients. “New developments and technologies give us the chance to think differently… they give us a broader vision,” observes Jim. And that leads directly to precise and premium metal fabrication and machining.
If you value innovation and excellence, contact us to join our Industry 4.0 journey and see where it takes your company.